Selecting the right tool presetter is crucial for any machine shop looking to optimise efficiency and achieve high-precision results.
From ensuring compatibility with current and future tooling, to evaluating service and support options, it is crucial to have the necessary knowledge to make an informed decision and unlock the full potential of a tool presetter on your shopfloor.
ZOLLER UK delivers world leading precision tool presetters, designed to suit the needs of every shopfloor regardless of floorspace, tooling requirements or budget.
Explore some of the key considerations when selecting a tool presetter below.
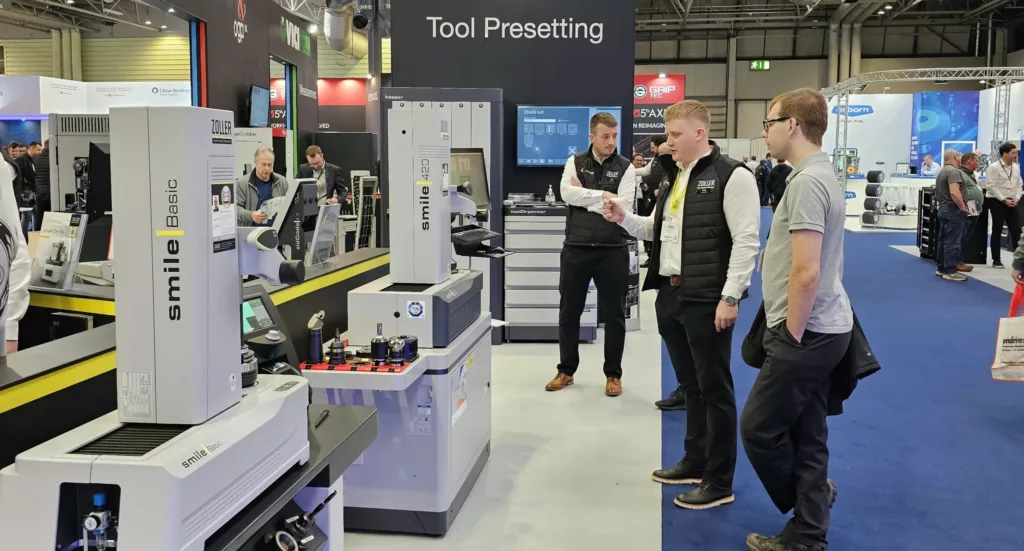
Key things to consider when selecting a tool presetter
Measurement range
The ideal presetter requires an extensive measurement range to accurately measure both large tools (long drills, wide facing cutters) and smaller tools (micro end mills).
Measurement accuracy
For optimal tooling accuracy, the presetter you select needs to meet the industry tolerance requirements. Some modern tool presetters can deliver micron-level accuracy, ideal for critical machining applications.
Tool holder compatibility
Shopfloors often utilise a diverse range of tools and tool types or suppliers may evolve over time. It’s crucial to select a tool presetter that accommodates current tool holders, whilst also offering the adaptability needed for potential future expansion.
Return on Investment (ROI)
When choosing a presetter, it is important to consider the return on investment (ROI) to maximise shop profitability. Utilise tools such as a productivity calculator to estimate your potential shopfloor savings.
Futureproofing
Manufacturing technology is constantly developing (software, AI, Smart Factories). Consider a presetters’ upgradeable software options and adaptable features to ensure its compatibility with any future advancements. This ensures the tool presetter remains a valuable asset on the shopfloor for years to come.
Service & support
Tool presetters are long-term investments requiring ongoing service and support. When choosing a supplier, consider the service options to ensure prompt responses and resolutions of any potential technical issues.
Integration into existing workflows
To ensure the seamless integration of the tool presetter into existing workflow with minimal disruptions, consider both its location on the shopfloor, as well as any operator training to maximise its use.
Tool Management Systems (TMS)
Integrating a TMS alongside your presetter allows comprehensive tool tracking and traceability across the shopfloor, streamlining operations and facilitating efficient tool management. This helps to maximise the benefits of investing in a tool presetter.
The ZOLLER tool presetting range
ZOLLER’s state-of-the-art offline tool presetting and measurement solutions are designed to maximise shopfloor productivity. By determining tool data offline, ZOLLER tool presetters ensure the highest level of tooling accuracy, saving valuable setup times and eliminating any potential errors.
Across the range of tool presetters, ZOLLER offers a range of different machines, with optional tool holders and software packages, as well as a variety of service and support options to ensure your tool presetter remains at peak performance.
Explore the range of state-of-the-art ZOLLER tool presetters below.
This tabletop presetting machine offers simplicity of operation, as well as fast, accurate tool presetting and measuring of standard tools offline.
The ZOLLER smile is an essential tool, guaranteeing high-level accuracy and repeatability by utilising its unique CNC spindle and auto-focus capabilities.
The venturion’s robust and modular design makes it the ideal tool presetting solution, providing maximum flexibility and precision, ensuring quality standards in manufacturing.
The redomatic offers a comprehensive solution for tool management that excels in the three disciplines of presetting, measuring, and heat-shrinking tools.
With a specially mounted revolving table, the hyperion quickly, accurately and reliably inspects tools to improve the efficiency, quality and productivity of parts.